Tuesday, January 20, 2009
Has anyone had issues when attempting to troubleshoot a Modicon Modbus Plus network?
If you've ever done this you know that it can be frustrating and time consuming.
There is an inexpensive tool to assist in this task.
It's manufactured by Delta Automation, Inc.
The part number is DA-MBP-100. It also comes with a detailed troubleshooting guide to lead you through the network to your problem quickly. It can also save you valuable time by determining if indeed you really have a network problem or some other issue.
Contact Delta at http://www.deltaautomation.com/ or phone at 804-236-2800.
Tuesday, July 25, 2006
Nuclear Power Plant Emergency Service Call
Friday we received a call from the local Power Company about a problem that they were having with one of their PLC systems at one of their two Nuclear Power plants in Virginia. A service call was scheduled for Saturday. After the lengthy security process, the field service engineer examined the system and found an intermittent remote I/O driver module. This part was exchanged and the system was up and running. Later that same day, the plant personnel replaced the same part with one that they had gotten from a sister plant. The system went down. They swapped the part back, but it was down hard. Another emergency call was made and our field engineer went back the plant. He arrived there at 11:30 PM. It was quickly determined that the problem was now in the fiber optic modem on the I/O communications that had failed. The plant had no spares. The Delta engineer made a call and another field engineer was dispatched with a new set of a different manufacturers fiber optic modems. These modems were delivered on-site. It was then discovered that the older fiber cable installed at the plant had SMA connectors, naturally the newer modems utilize St type connections. Luckily the Delta Automation service van is stocked with all sorts of these types of items. Inside there were enough adapters to properly connect the modems to the system. The system was up and running properly immediately. At 3 AM, all was well at the plant.
This is the type of service that our clients have come to expect from Delta Automation, Inc.
This is the type of service that our clients have come to expect from Delta Automation, Inc.
Tuesday, May 16, 2006
Industrial Network Certifications
The Importance of
Network Certification
In the Plant Environment
By
Robert S.Culley III
With the advent of today’s high-speed communications and plant floor level of information exchange, the necessity of reliable, error free communications is essential. This is especially important when considering the environment of paper making machines. Temperature and humidity extremes, vibration, electromagnetic or radio frequency interference and frequent wash-downs can all have an adverse impact upon the various components that can make up a complete system.
The actual media, cabling, connectors, taps, etc. are often overlooked when installing or even designing a system. When having industrial networks installed, most large corporations allow their contractors to install them "as built". This can and often does allow sub-standard components to be used. Even when the contract drawings specify a particular part or component, the contractor may depend on a particular distributor to make a substitution. Unfortunately, substitutions are not always equivalent to what is specified. These seemingly small deviations in specifications have a cumulative effect. A small change in cable specification coupled with other factors such as distance, number of nodes, noise levels or connector quality and fit, can result in a network which performs poorly. Typically the installing contractor does not have access to the proper installation instructions, which are usually included along with the equipment from the manufacturer. The panel assembly personnel or the department which unpacks the equipment often discards these instructions. In some cases the salesperson rather than an experienced technician or engineer attempts to instruct the installers on the finer points of installation.
The lack of performance of the network does not always manifest itself in an obvious way. Often there are intermittent application symptoms. These may include, losing data, dropping out of discreet points, inability to tightly control loops or just inexplicable problems.
By examining these variables individually, we can begin to understand their effect on the many different components that can contribute to a failure.
The range of temperature swings which are common at the paper-making machine does affect the cabling. All manufacturers have a specified temperature range for each type of cable. If the cable is installed without regard to these specifications, the life of the cable will be short. Even when installed at or near the limits of the manufacturers recommendations, its life expectancy can be significantly reduced. If installing communications cable in areas which experience these types of extremes, consult with the manufacturer for a "life de-rating specification". The actual physical movement of the cable causes the dielectric to degrade and in coax cable, any movement which changes the relative position between the center conductor and the shielding, changes the cables characteristic impedance. Impedance changes will affect the shape of the waveform being transmitted and improper triggering or framing may result. Another consideration with cabling and temperature changes is the expansion and contraction with reference to the connectors. If the cable is installed during a high temperature cycle, when it cools and shrinks, it may pull out of the connectors completely. Or worse yet, just pull out enough to make communications intermittent and very difficult to pinpoint. This is usually corrected by making sure that sufficient service loops remain in the cable runs.
If your system utilizes taps, splitters, or some other means of branching connectivity, pay attention to the product temperature specification as well. It is highly recommended that these types of devices, although usually passive, not be installed in those areas if possible.
The water and humidity surrounding the paper process can act as a catalyst to create special problems in the communication system. Most obvious is the introduction of water itself into the connections, devices and cabling. Any water will disrupt the proper transfer of signals and data. These usually manifest themselves as intermittent failures which can be very time consuming and costly to locate. The proper method of avoiding this type of problem is to consider the effects of water on the system during the installation phases of the cable. Water-resistant cable should be utilized and installed in water-resistant metallic conduit, which will provide RFI and EMI shielding as well. Drip loops should be at all cable to cabinet entrances to allow any moisture or condensation to drip harmlessly away from any devices. It is advisable to utilize connectors which seal the cable to the back of the connector. Further reliability can be achieved by installing boots on all connectors. This not only prevents moisture from entering, but also inhibits airborne contaminants from damaging the conductors.
The amount of vibration experienced on any paper machine will vary greatly with product type and speed. This vibration has a cumulative affect on components over time. Vibration affects cables in much the same fashion as conductors are by temperature induced expansion and contraction degradation to the dielectric and its relative positioning to the conductors. The only measure of prevention is to remotely mount any components away from the vibration source. In the real world environment it is not always practical to accomplish this. It must be remembered that locations where vibrations exist, should be the first place to be examined if problems arise. Check for loose connections, relaxed crimps, loose grounding or bonding, and device failures.
The most frustrating problem to remedy is that of electrical noise. Borne by electromagnetic, or radio frequency interference. These problems are particularly troublesome to communication systems. Typically, these anomalies arise over time as more and more noise generating equipment is added through process and system upgrades. An example of this is variable frequency drives. Older machines may have had their communications systems working flawlessly for years, only to attempt a restart after a shutdown and find that the communications network is not functioning properly. Upon examination of the system with test equipment, it is usually found that a new drive installation, unrelated directly with the communication network was upgraded during this shutdown period. The most efficient way to reduce noise interference is to control it at the source through proper ground bonding and short motor leads. Sometimes this is not possible. In which case, another method is to install multi-shield (commonly called quad shield) cable to further reduce the noise level with reference to the data on the cable. Utilizing metallic conduit can further enhance this. It is common in these instances to encounter reluctance from the "decision-makers" to install new cabling on a system that has "worked for years". It must be explained that the original cabling does not have sufficient shielding to attenuate noise to within tolerable levels of the newer more modern equipment. Usually, a temporary multi-shield cable can be placed in the system outside of the noisy area to demonstrate the reduction of data errors or communication problems. Once the noise reduction theory is proven, a plan can then be discussed to replace, or re-route the cabling.
Should a network problem be suspected, the first action is to utilize the network protocol diagnostic software usually provided by the manufacturer of the communication nodes to determine if indeed there is a problem. In reality, all networks should have in place, a software monitor to alert users of any degradation or errors on the network so that action may be taken to prevent a catastrophic failure.
Once that it is determined that errors do exist on the network, a plan should be developed to investigate and correct any defects. This plan should include, a visual inspection of all components, a Time Domain Reflectometer test, a dB loss test (if applicable), a drop out test (headroom), an overall impedance check and monitor for any noise. Once these tests are done, the data should be analyzed, and be compared to the manufacturers specifications to determine if the system is operating within acceptable performance tolerances. This is referred to as a network certification. It is very rare for a system to meet all of the specifications and still have a problem. If a problem exists on a certified network, the trouble usually resides in the actual application or possibly a problem within the software/firmware of the nodes themselves.
Most if not all network problems can be eliminated or reduced during the design and installation phases. The manufacturers specifications must be adhered to at all times. It is the responsibility of the installing contractor to utilize the best installation techniques such as monitoring the minimum bending radius of the cable, not exceeding the pulling limits, routing with high voltage limits and using conduit effectively for noise elimination. These aforementioned items are sometimes costly to implement during installation but are cost prohibitive to implement at a later time when production uptime is critical.
If you would like more information on Network Certification and maintenance, please contact Delta Automation Inc. at 1-888-PC-DELTA or E-mail at PLC@Deltaautomation.com.
Robert S. Culley III
Monday, May 15, 2006
Opening post about PLC's
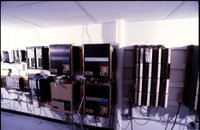
From time to time it may include other non-industrial information just for some diversity.
My background with PLC's includes a lengthy employment with the manufacturer of the Modicon PLC line. I traveled the world over supporting these PLC systems, visiting 5 of the 7 continents and working in just about every kind of factory, plant and industrial type site imaginable.